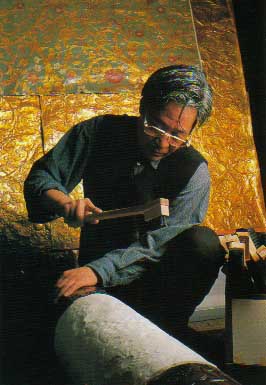 |
Takashi Ueda
Representative of Kinkarakami
Instiute
1934 Born in Kyoto
1985 Establishs kinkarakmi
Institute
the only one Kinkarakami
production technology holder
in the world.
Bearer of Technizues
Selected for Preservation by
the Agency for Cultural
Affairs Japan
4-1-20 mejiro Toyoshima-ku
Tokyo-to
℡ 03-3565-0169
Inquiry
kinkarakami@live.jp
kinkarakmi Institute
Web Manager
Koji Ebata |
Kinkarakami History of
reproduces
1987 Nippon Yusen
Company
in Otaru |
 |
1990 Tokyo Art Theater |
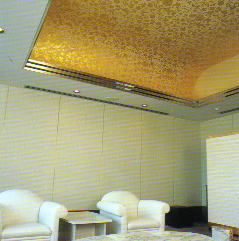 |
I think Kinkarakami was made by
the tradition of Europe and
examples of traditional
craftsmanship of Japan. and
It is Japanese artistic
production not known so much
in the world.

|
|
Various art works of Kinkarakami If the image is clicked, you can see a larger image.
Kinkarakami(gilded , embossed and colored paper) is an imitation of gilded leather(cuoi d'oro)used
as an interior material in Europe before. Kinkarakami is a gorgeous wallpaper. Kinkarakami
received high acclaim in Europe and America at the Meiji era(1868~1912), and export was done
actively.The room covered with Kinkarakami remains it is in Paleis Het Loo in the Netherlands.
However, it declined to about the start at the Showa era(1926~1989 and it became a lost
craft. After World War 2, some attempts were made at its reproduction, but these ended in vain.
Takashi Ueda thus bccame determined to undertake the difficult task of reviving the lost
handicraft of a century ago. |
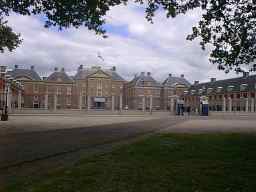 |
|
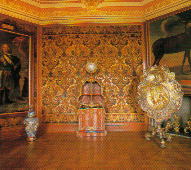 |
Paleis Het Loo in the Netherlands |
The room covered with
Kinkarakami |
Castle Moritzburg in Geamany
remains the room covered
with gilded leather(cuoi d'oro) |
A project to restore the wallpaper for the Otaru Offilce of Nippon Yusen Company
brought about such an opportunity. As it turned out, the original wallpaper was made
of kinkarakami, and the National Research Institute for Cultural Properties
and the Japanese Association for the Conservation of' Architectural Monuments began
a search for someone able to restore this craft which would otherwise be completely
lost. Tskashi Ueda, who was at the time based in Kyoto dealing in art publishing
associated with cultural heritage and who was familiar with the techniques of making
Japanese paper (washi) and metallic foils, was asked to tackle this task. He thought: 'If
nobody else can do it. then I shall. He began to search for a method to reproduce
Japanese leather paper while getting some expert advice. It took him two years to
reproduce it in a satisfactory way. During these two years, Ueda became fascinated with
Kinkarakami and its exotic history, and has continued to produce it even after
successfully restoring the wallpaper for the Otaru building in 1980. Since then, Ueda's
technique of producing Kinkarakami from the Meiji and Taisho piriods has been
indispensable for Important Cultural Property all across Japan. He calls
his niwly creatcd products 'Kinkarakami,' thus distinguishing them from the now lost,
original 'Kinkarakami' products. |
Pridycion process of Kinkarakami
Ueda's production process is as follows. First, thc 'washi' paper is made by.joining
handmade Kozo paper and Mitsumata paper. This papcr, made of natural material of'
botanical fibers, automatically adjusts to the humidity of the room while also blocking
heat. First, tin or silver or gold foil is adhered to the washi paper, and then it is sprayed
with water. The paper is then wound onto a woodblock roller and beaten with a brush fbr
four to five hours until the design is firmly and evenly applied. This also helps the paper
and foil to merge well and reinforce the paper. The cherrywood roller makes deep and yet
familiar sounds when beaten. The paper is then dried, backing paper is applied, and the
surface design is tinted with colorcd 'urushi' Iacquer and oil paints, etc. A final coating of
clear varnish turns the tin foil into golden colour. Finally, persimmon extract is applied a
few times onto the back of the paper to make it waterproof. The main differencc between
this method and that of the past is that in the past metallic foil was applied after the paper
was embossed. Ueda's method is officially recorded at the Edo-Tokyo Museum (Tokyo) as
an art of' Edo craftspeople. The process is a combination of many defferent crafts.
It takes half a month to complete a 60sq cm piece of wallpaper. |
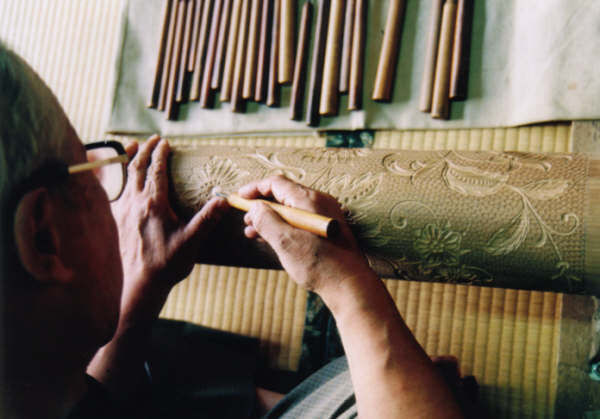 |
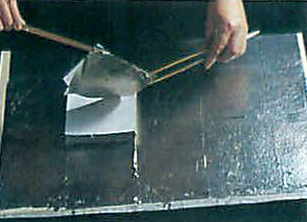 |
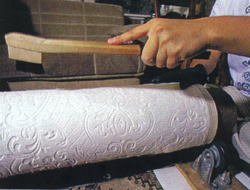 |
makeing woodblock roll |
adhering silver foil |
beateing brush |
2007 Demonstration of making Kinkarakami in London
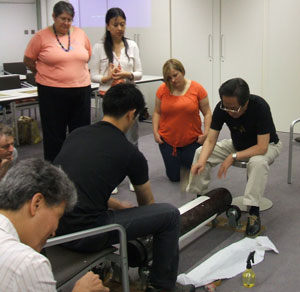 |
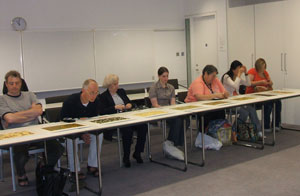 |
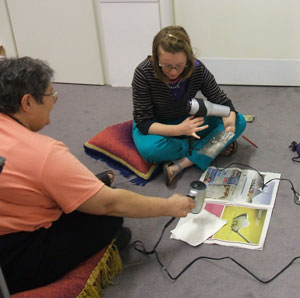 |
Demonstration inBritish
Museum |
a presentation of Kinkarakami |
coloring Kinkarakami |
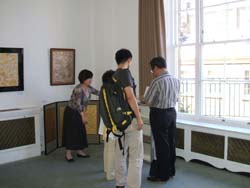 |
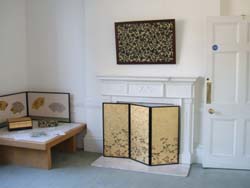 |
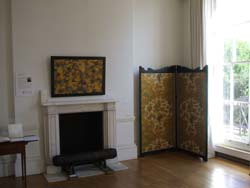 |
One-man show in London |
One-man show in London |
One-man show in London |
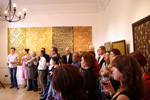 |
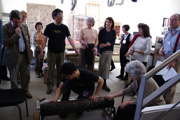 |
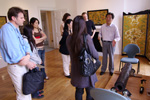 |
One-man show in London |
preparing Demonstration |
a presentation of Kinkarakam |
|